We are constantly working to optimize our “QCD” (Q = quality, C = cost, and D = delivery time) and to develop the new machining technologies that environmentally friendly manufacturing depends on.
The Production Engineering Division, which plays a fundamental role in FUJI OOZX Group’s manufacturing, has three major roles.
1Promoting pre-production processes for new products
The Production Engineering Division, making use of various information inputs from the Design section, creates processes that make it possible to mass produce products and optimize quality, costs, and delivery time while maintaining our all-important design quality. They also conduct other preparation activities related to the start of mass production in compliance with IATF 16949.
2Bringing about processes that contribute to Q, C, and D optimization
We are streamlining the manufacturing processes on production lines already in operation.
This is accomplished by introducing new equipment, reviewing manufacturing conditions, and extending the service lives of jigs and tools, thereby improving the efficiency of processes.
Our goals are to completely revamp FUJI OOZX’s manufacturing system and optimize its QCD. In the process, we are also promoting efficient process improvement, taking advantage of the use of cutting-edge simulation technology, and IoT & AI technology.
3Developing new manufacturing technologies as bases for the development of new products
The Production Engineering Division is working to develop new manufacturing methods that are appropriate for new products, making full use of our knowledge -- accumulated in the manufacture of engine valves, retainers, and cotters -- related to forming (hot and cold), heat treatment, machining (grinding and drilling), and welding (plasma welding, friction welding,
and electric resistance welding). This division is working in cooperation with the design and manufacturing sections, fostering flexible ideas that are not bound by conventional concepts and creating a bold mindset that is not held back by a fear of making mistakes. We enthusiastically promote young engineers to participate in this project, because taking part in these activities will give them the background to become our next generation of highly skilled and professional engineers.
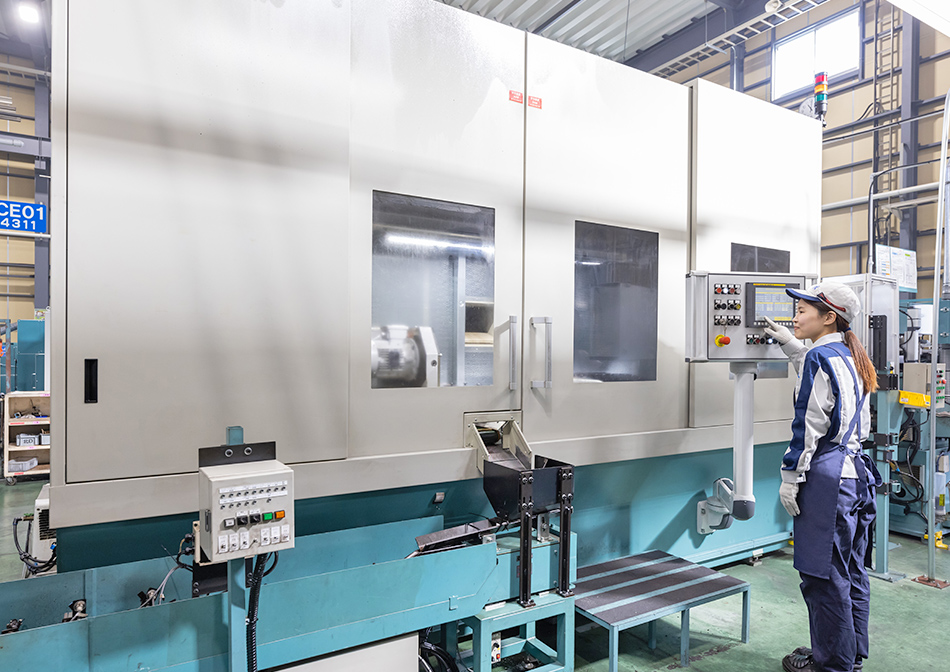
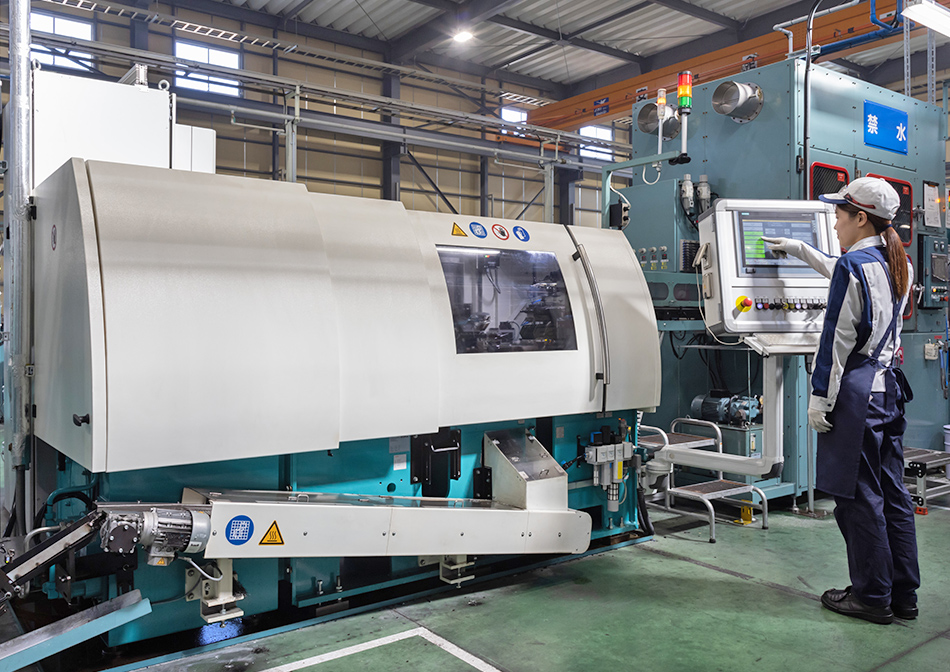
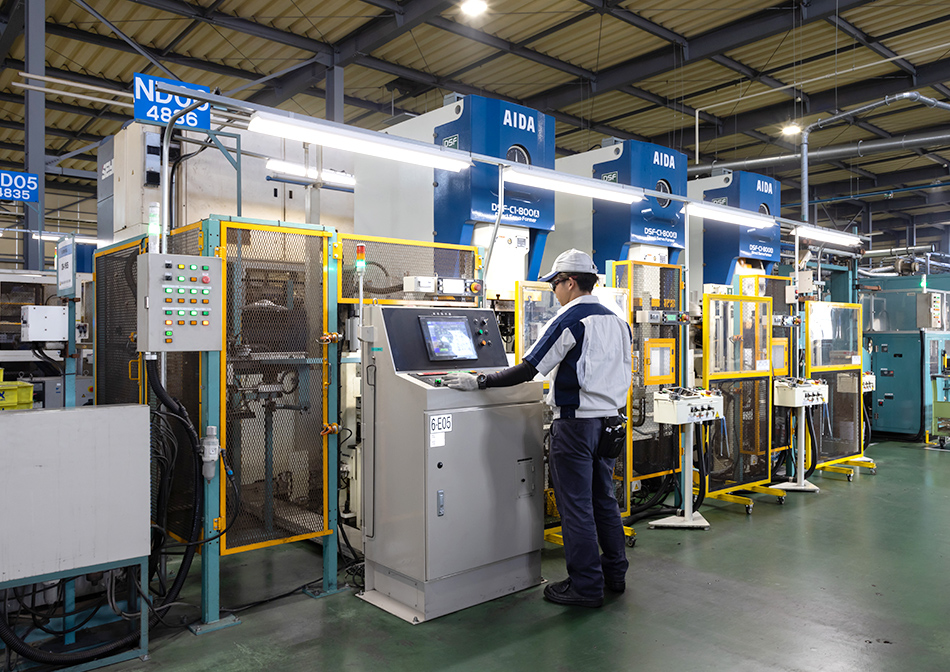
Production Equipment
1Forming
-
Hot forming
Our engine valves are hot-extruded using a screw press. In this method the entire workpiece is heated and forged into a valve shape. This economical method, making efficient use of the forging heat, means later quenching and solution treatment becomes unnecessary for most types of material. In recent years, we have also introduced simulation technology in the mold design process, which enables us to start mass production quickly.
-
Cold forming
Retainers and the hollow portions of hollow-head valves are cold forged using a crank press. Cotters are formed by being drawn from coiled material.
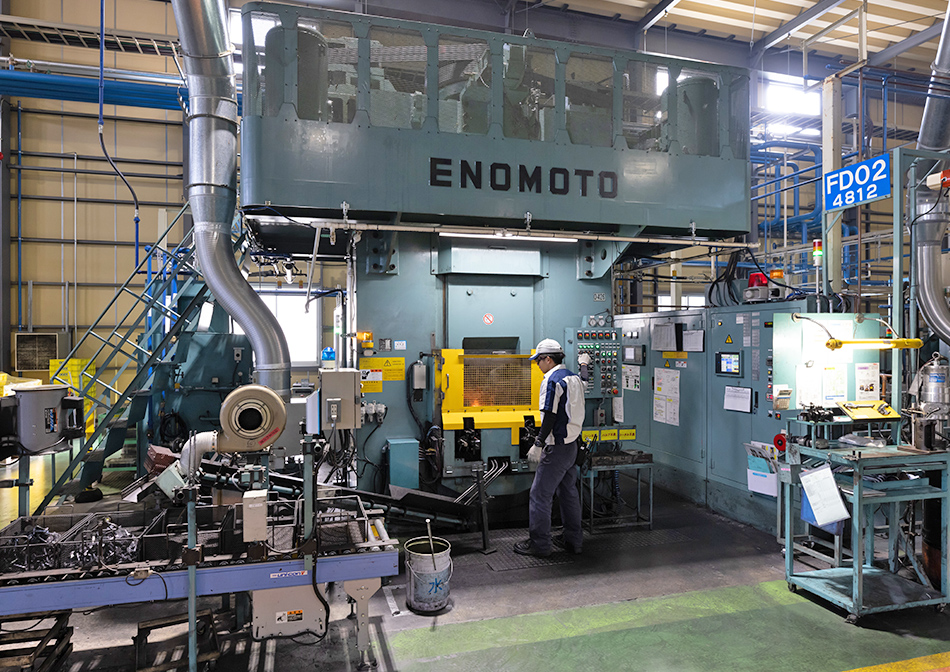
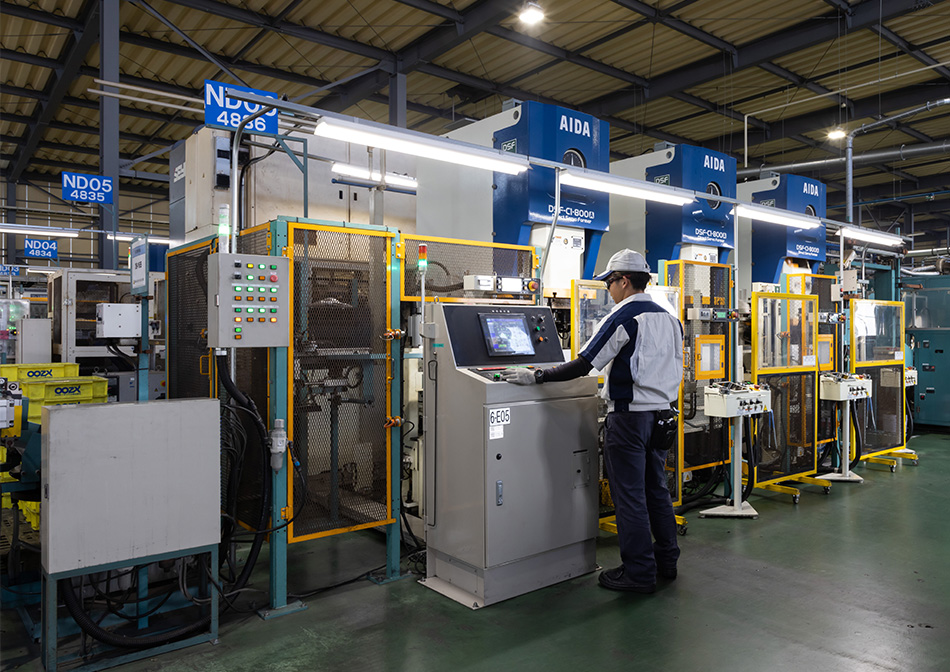
2Heat treatment
We use three furnace types for our heat treatment processes: atmospheric, controlled-atmospheric and vacuum furnaces. Each of these can be either batch or continuous operation. We have introduced Daido Steel's Syncro Therm into our production system, which is a continuous vacuum furnace. It provides fully automated heat-treatment operation, from workpiece jig setup to furnace unloading.
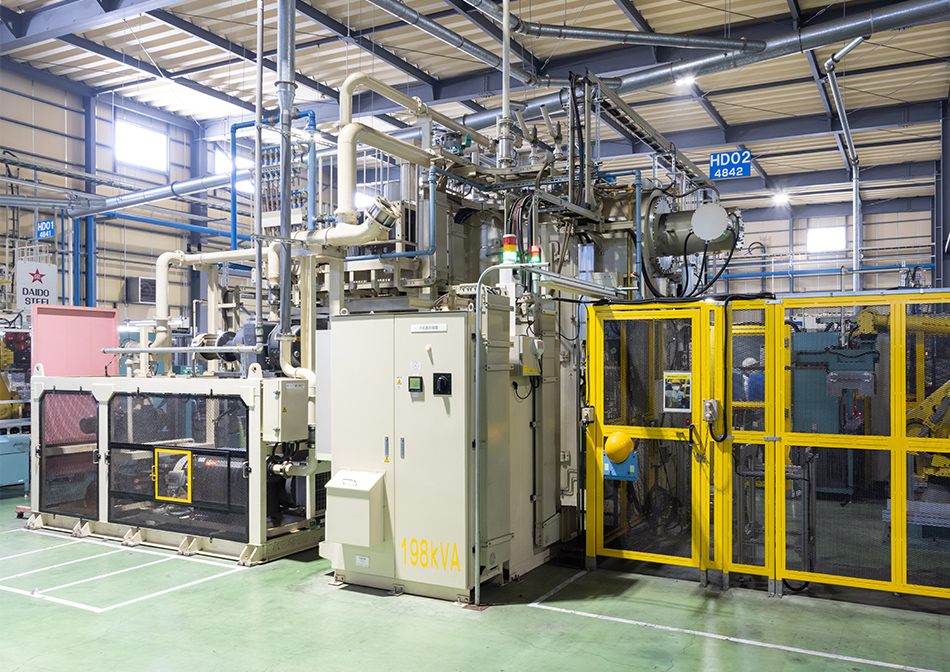
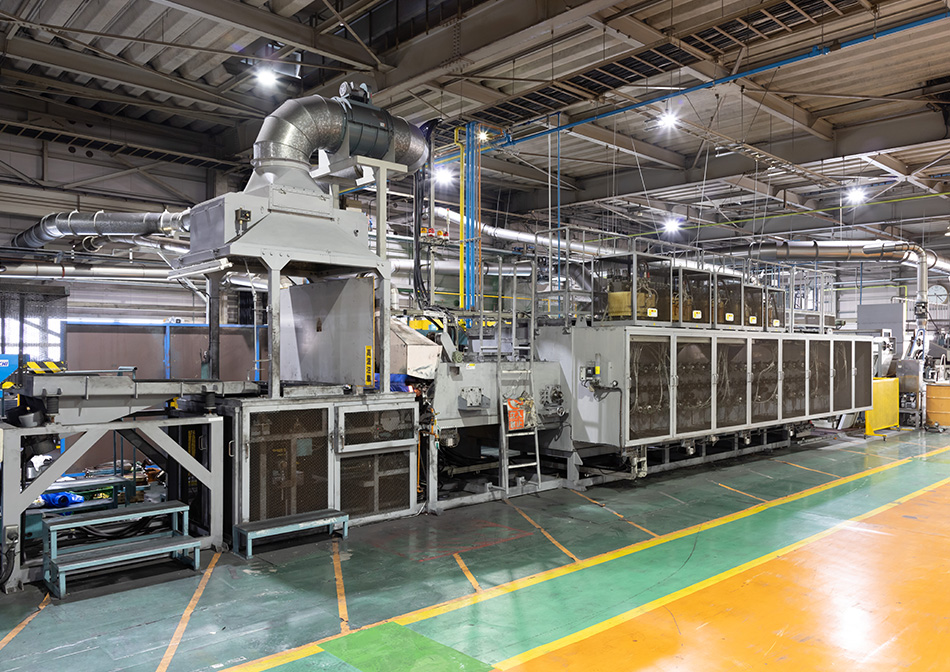
3Machining
-
Grinding
The MUG (Multi Use Grinder) is primarily used to shape engine valves. This device was designed in-house, and makes use of long-life grindstones.
-
Drilling
A drill machine is used to hollow out the stems of engine valves. All drills are ground in-house to form our original cutting edges, designed to provide long drill life.
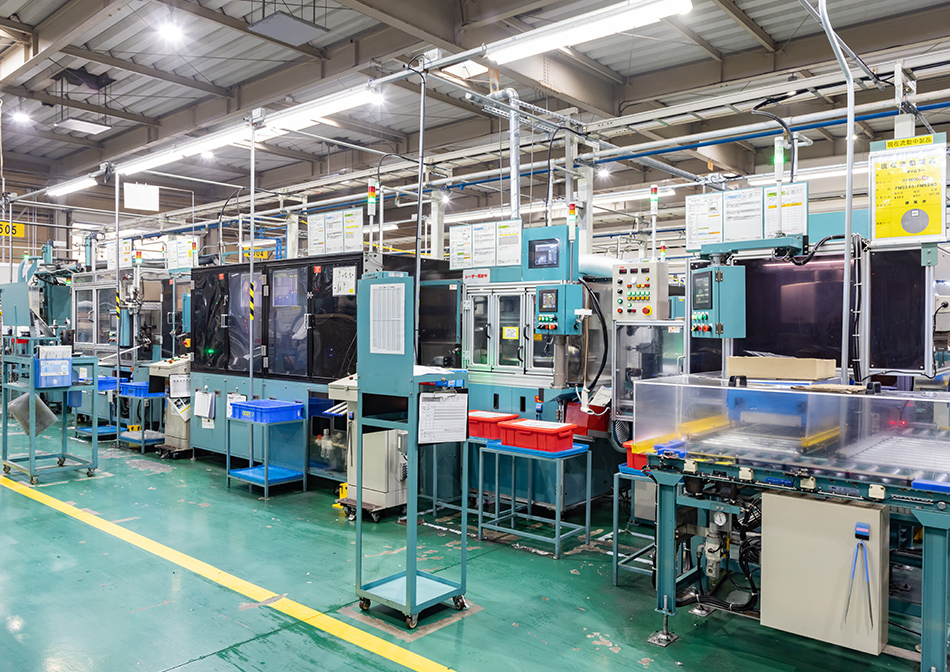
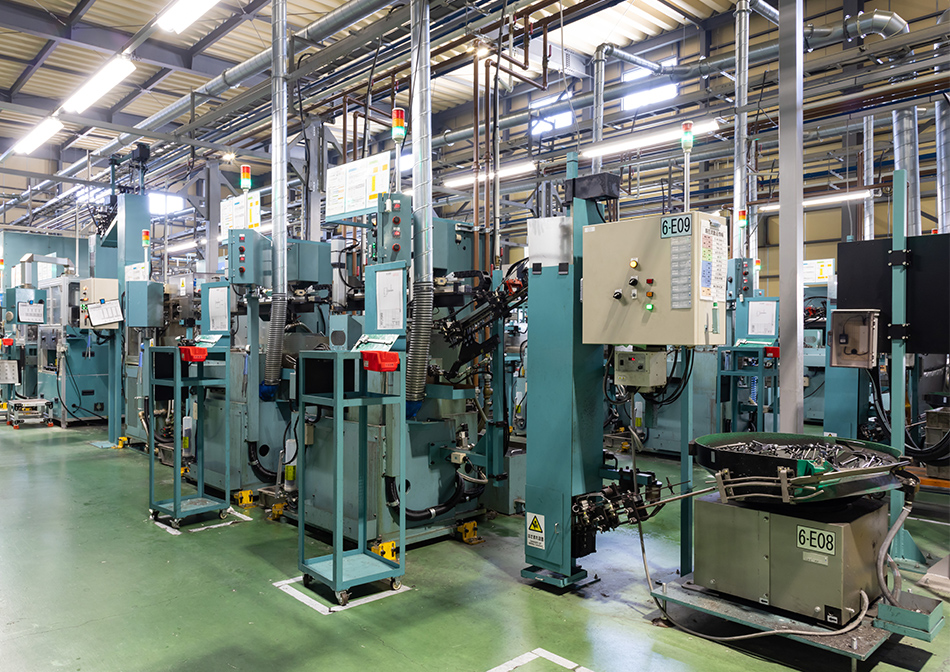
4Welding
-
Plasma welding
A hard metal called Stellite is welded to the valve face, using a welding machine called a
PPW (Plasma Powder Welding ) to improve the wear resistance of the valve face. -
Friction welding
In friction welding, heat is generated on the valve stem through mechanical friction between workpieces of either similar or dissimilar materials, and the heat fuses the parts together.
-
Electric resistance welding
In electric resistance welding, a strong current is applied to one of the valve stem ends, which generates enough heat to fuse a dissimilar material to it.
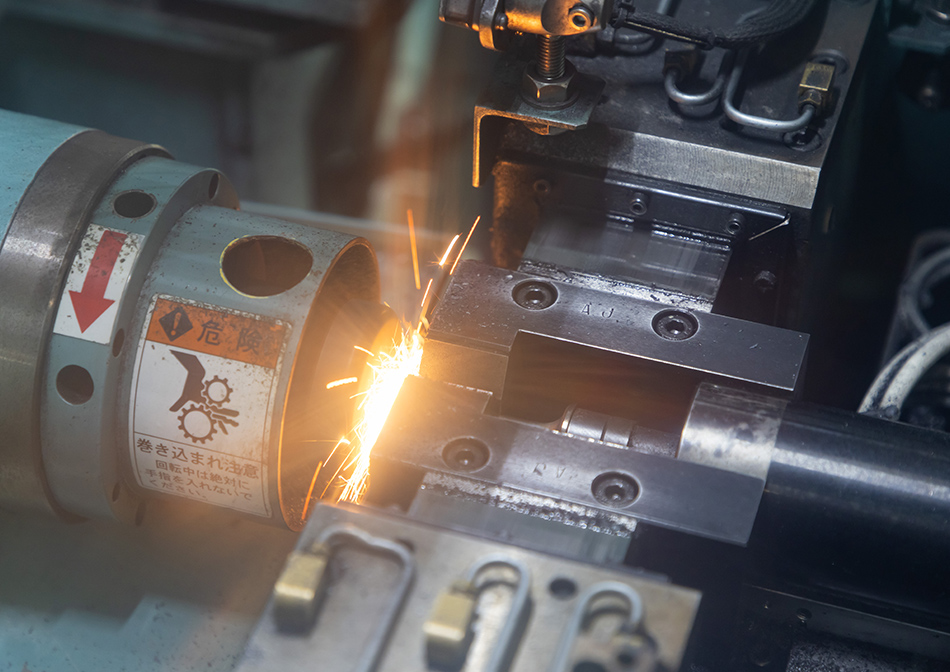
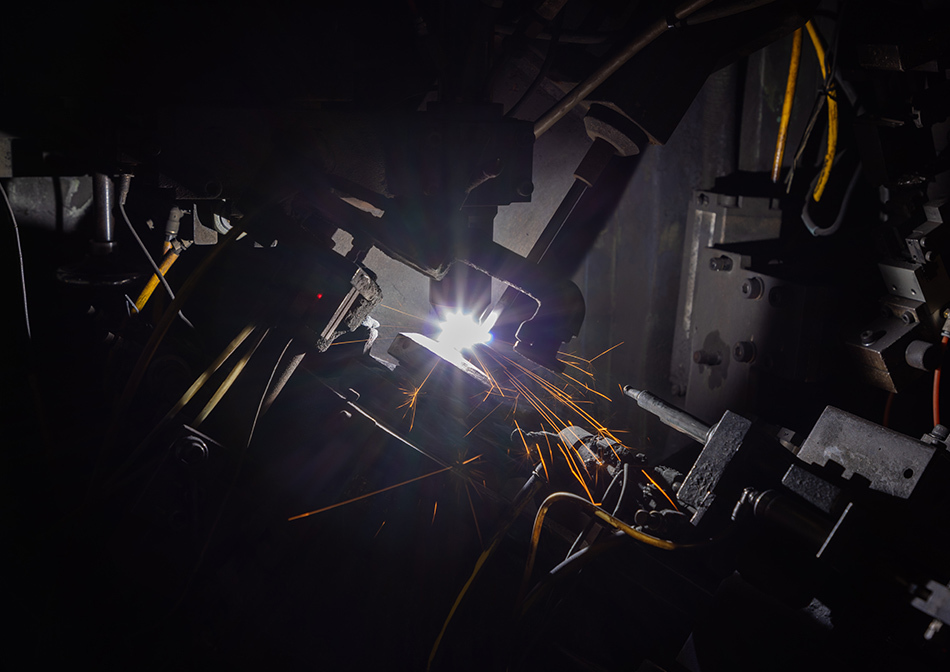